Advanced Fasteners and Machining Techniques for Custom-made Production
Advanced Fasteners and Machining Techniques for Custom-made Production
Blog Article
Revealing the Ins And Outs of Fasteners and Machining Procedures for Optimum Performance
In the world of design and production, the choice of fasteners and the complexities of machining processes play an essential role in identifying the supreme performance and durability of a product. From the seemingly straightforward task of choosing the ideal sort of bolt to the complicated precision machining techniques used, every step in this procedure demands careful interest to detail. As we begin on this expedition right into the world of bolts and machining, we will uncover the refined yet critical factors that can substantially influence the efficiency and quality of the final product, shedding light on the often ignored facets that can make all the difference in accomplishing optimum performance.
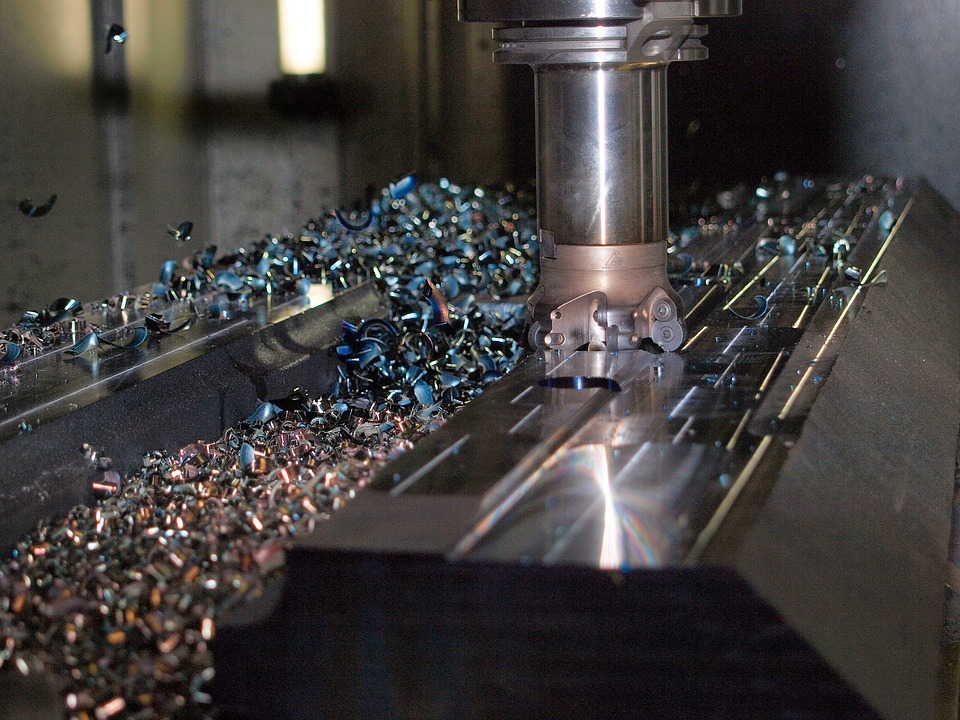
Importance of Proper Fastener Selection
Picking the ideal fasteners is important in making certain the architectural honesty and long life of any type of mechanical setting up. Bolts play a basic role in holding parts together securely, with the ideal choice contributing substantially to the general efficiency and integrity of the assembly. When picking fasteners, elements such as product compatibility, environmental problems, load-bearing ability, and convenience of installment need to be thoroughly taken into consideration to guarantee optimal performance.
Inappropriate bolt choice can bring about an array of issues, consisting of helping to loosen, corrosion, and also structural failure. Making use of fasteners that are not matched to the details requirements of the assembly can endanger its performance and pose safety and security dangers. Consequently, designers and engineers should carefully evaluate the application needs and select bolts that fulfill or exceed the needed criteria and specifications.
Moreover, the appropriate bolt selection procedure includes evaluating the joint design, prepared for loads, vibration levels, and possible thermal development or contraction to ensure that the chosen bolts can hold up against the operating problems successfully. By prioritizing proper bolt choice, makers can boost the quality, sturdiness, and efficiency of their mechanical settings up.
Types and Features of Bolts
A necessary facet of mechanical settings up hinges on understanding the varied types and one-of-a-kind qualities of fasteners made use of in various industrial applications. Bolts are vital parts that hold frameworks with each other, ensuring security and functionality. There is a variety of fasteners readily available, each designed for specific functions based on the application requirements. Usual kinds of fasteners consist of screws, screws, nuts, washers, pins, and rivets.
Screws are threaded bolts that are commonly used to join 2 or more elements with each other. Nuts are inside threaded bolts that mate with screws to hold elements together. Washing machines are slim plates that distribute the load of a bolt, stopping damages to the product being attached.
Comprehending the attributes of each kind of bolt is crucial for selecting the ideal one for a particular application, making sure optimal efficiency and read this reliability of the mechanical assembly. Fasteners and Machining.
Accuracy Machining Strategies for Effectiveness
The complex style needs of various bolts demand using precision machining strategies for optimal efficiency in producing processes. One of the key methods utilized in accuracy machining is Computer Numerical Control (CNC) machining, which allows high levels of accuracy and repeatability in the production of fasteners.
In enhancement to CNC machining, other precision techniques such as grinding, milling, and transforming are typically utilized to accomplish the limited tolerances needed for fasteners. These methods allow makers to develop fasteners you can check here with smooth surface areas, exact dimensions, and high architectural honesty. By utilizing precision machining methods, makers can boost the high quality of bolts, minimize product waste, and enhance overall manufacturing effectiveness. The usage of advanced machining processes aids make certain that bolts satisfy sector criteria and consumer assumptions for performance and reliability.
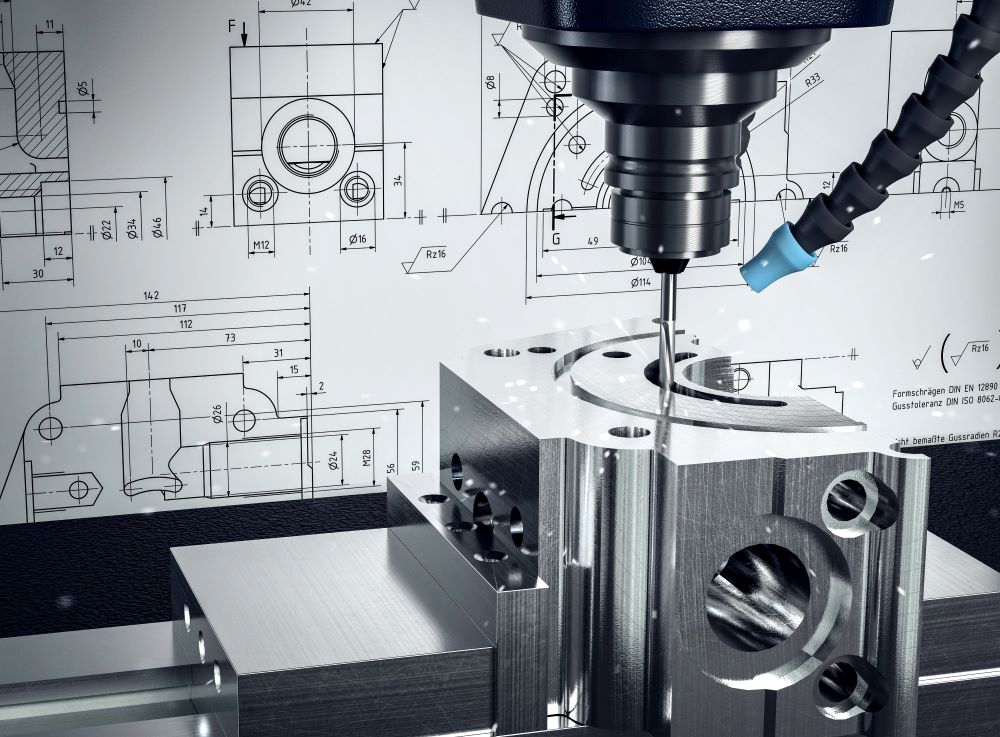
Variables Affecting Machining Process Efficiency
Different variables play a significant function in determining the performance of machining procedures in the manufacturing of fasteners. Optimizing these criteria based on the certain needs of the fastener being produced is crucial to accomplishing specific and cost-effective machining.
Machine rigidness and security also play a vital function in figuring out machining procedure performance. An experienced driver can make real-time changes, troubleshoot issues effectively, and make sure that the machining procedure runs smoothly, eventually impacting the last top quality of the fastener.

High Quality Control Steps in Production
Variables affecting machining process performance, such as cutting tool selection and maker security, straight influence the application of quality control procedures in production. Routine upkeep of machining equipment is likewise vital to promote top quality control. By sticking to strict high quality control steps, producers can enhance consumer contentment, construct a track record for dependability, and inevitably achieve optimal performance in their machining procedures.
Verdict
Finally, choosing the ideal bolts and making use of precision machining methods are crucial for optimum efficiency in manufacturing processes. Understanding the kinds and qualities of fasteners, along with aspects influencing machining process efficiency, can result in enhanced efficiency and quality assurance actions. By paying interest to these ins and outs, manufacturers can attain higher levels of performance and her response dependability in their products.
In the world of design and production, the choice of fasteners and the details of machining processes play a pivotal function in figuring out the ultimate performance and toughness of a product (Fasteners and Machining). One of the main strategies utilized in precision machining is Computer system Numerical Control (CNC) machining, which enables high levels of accuracy and repeatability in the manufacturing of bolts. The usage of innovative machining procedures aids make sure that fasteners satisfy market criteria and client expectations for efficiency and integrity
In final thought, choosing the ideal fasteners and making use of precision machining techniques are vital for optimum efficiency in manufacturing processes. Comprehending the kinds and features of bolts, along with aspects influencing machining process performance, can lead to enhanced effectiveness and high quality control procedures.
Report this page